How does a WMS system increase shipping accuracy?
- sonali negi
- Mar 25
- 6 min read
Updated: Apr 11
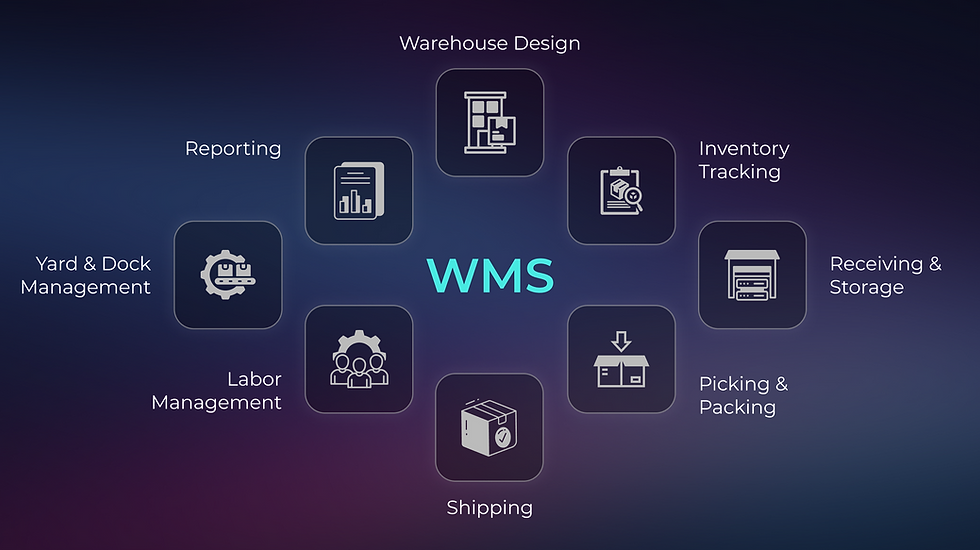
Have you ever thought about how speed and accuracy in shipping affect today’s competitive landscape? If you manage a warehouse, you probably understand that accurate and fast delivery is essential to business success. After all, who doesn’t want to receive their orders without errors or delays?
In a busy warehouse where hundreds of products are stored, organized, and shipped daily, when a customer places an order, you not only have to locate it in stock but also ensure flawless delivery.
In this context, shipping accuracy has a direct impact on customer satisfaction and financial performance. An error or delay in delivery can damage customer loyalty and brand reputation. This is where the WMS (Warehouse Management System) system comes in handy, ensuring process automation, workforce optimization, and workflow coordination in the warehouse.
Fewer shipping errors mean greater savings in time and resources, resulting in high performance and a good reputation in the market. Want to know how WMS can transform your warehouse and exceed customer expectations?
10 ways WMS can revolutionize shipping and boost your business.
1- Reduction of errors in picking and returns
One of the great benefits of the WMS system is to increase picking accuracy , which directly affects the quality of the shipping process.
By employing advanced real-time inventory tracking and management technology, a WMS provides complete visibility into the location and status of each item. This means operators can pick items accurately, avoiding incorrect selection of products or wasting time searching for “lost” stock.
Another advantage is that the system assigns the best pickers, maps intelligent picking routes, and defines methods for each order. The WMS can also group orders by common characteristics, such as destination, priority, or size, minimizing travel time and maximizing efficiency.
What's more: by integrating with barcode collectors, RFID, pick-to-light , voice picking and other technologies, the WMS is able to guarantee extremely high precision in the selection process, as well as great speed.
The result is a significant reduction in shipping errors, which translates into fewer returns, resource savings, and, most importantly, satisfied customers.
2- Second-order conference
After the order has been picked, many WMS systems implement a second item check in the shipping area. This involves a thorough review of the selected items to ensure they are perfectly aligned with the customer's specifications before shipping.
By operating the WMS system during shipping, accuracy is ensured, avoiding common errors such as choosing the wrong item or the wrong quantity. In addition, the system incorporates quality control checks and ensures that products are in impeccable condition before final shipment, thus minimizing the risk of sending damaged items and future returns.
3 – Adequate packaging and volume cubing
The WMS has a feature that helps determine the ideal packaging size for each order. This is called “volume cubing”.
When the complete order arrives for shipping, the system indicates the size and type of material to be used for packaging and shipping to the customer. This prevents packaging errors, damage during transport, and wasted space in boxes and pallets, reducing shipping costs.
4- Label generation
Another great advantage of WMS for shipping is the automatic generation of shipping labels, which contain detailed information about the products, recipients, and delivery locations. These labels ensure that the right products arrive at the right destination.
5- Automation and accurate document generation
In a warehouse, managing a huge amount of information is a challenging task. This is where automation comes into play, eliminating the need for time-consuming manual processes such as filling out forms and checking compliance, enabling a more streamlined and efficient workflow.
The WMS system plays an important role in this scenario. It automates the generation of shipping documents and compliance requirements. In practice, this means that the WMS generates and prints the necessary documents for each order, such as invoices, packing slips, bills of lading, customs forms, and certificates of origin.
This not only ensures regulatory compliance but also meets industry, market, and customer standards and protocols, thus avoiding legal issues and delivery delays.
Additionally, automation through the WMS system significantly reduces paperwork, making the shipping process more efficient, sustainable, and easy to manage.
6- Load optimization
Load optimization and consolidation are important for warehouses for several reasons. First, load consolidation is a smart strategy for reducing shipping costs. Imagine bundling multiple orders into a single shipment, filling every inch of your trucks efficiently. Not only does this save space, but it also reduces transportation costs. After all, who wouldn’t want to save on shipping costs?
Second, delivering multiple orders in a single shipment is a real shortcut to saving time and resources. When you don’t have to deal with different carriers and shipping partners, everything becomes more efficient, from logistics to shipping.
In this way, the WMS system offers valuable support at this stage. It allows for the intelligent grouping of loads through an integrated system, combining orders that have similar delivery dates and locations. This makes truck loading more efficient. The system also supports the processing of split loads, which enables the movement of stock to different warehouses or satellite locations, optimizing distribution.
Load consolidation brings several practical benefits to the warehouse, such as:
Significant savings on shipping costs.
Increased operational efficiency.
Better use of available resources.
Agility in shipping.
High customer satisfaction due to faster and more accurate deliveries.
7- Integration with carriers
Carrier integration is another great benefit of WMS for shipping. The software can connect directly to carrier systems, couriers, and third-party logistics providers, providing real-time visibility into the status and location of shipments. This functionality allows for detailed tracking of ongoing deliveries.
Additionally, the WMS system promotes efficient communication by sending confirmation emails and delivery notifications to customers and interested parties, keeping everyone constantly updated on the status of orders.
Effective integration with carriers brings notable practical benefits to the warehouse, including increased efficiency by optimizing order flow, reducing transit time, increasing delivery speeds, and promoting transparency and accountability across the supply chain, resulting in more reliable operations.
8- Integration with other systems
Integration with other workflow systems eliminates the need for time-consuming manual work and reduces duplication of tasks. Data flows seamlessly between different software, streamlining the ordering and shipping process.
Technology involved in integration may include ERP ( Enterprise Resource Planning ), CRM ( Customer Relationship Management ), e-commerce systems, accounting, and others. The WMS plays a key role in communicating and exchanging data with these software programs, ensuring that all order information is consistent, accurate, and up-to-date across all systems.
9- Returns management
Did you know that an effective reverse logistics strategy is essential for market competitiveness? This strategy directly influences customer satisfaction and significantly reduces operating costs. This is because modern consumers value the convenience and reliability of online shopping, which allows them to make exchanges and returns without difficulty.
In this scenario, the WMS system appears, once again, as a great ally. First, because the picking accuracy provided by the software will help reduce return rates. Second, because the WMS ensures that returned products are handled properly and reintegrated into stock without errors.
This automation of directing returned products to specific storage areas optimizes the sorting process, saving time and resources.
What’s more, WMS also provides insights that allow companies to identify return trends and address recurring issues. This makes reverse logistics management complete and highly effective.
10- Continuous monitoring of costs and performance
It’s no secret that the key to a warehouse’s success lies in its direct impact on the operational efficiency and profitability of the business. For this reason, understanding and controlling overall investments is necessary so that an operation can optimize its financial resources, avoiding waste and inappropriate allocations.
And this is where WMS comes in to provide full support. In the specific case of order dispatch, the system has a series of dashboards and KPIs that allow you to collect and store crucial data, such as order volume, fulfillment rate, accuracy rate, on-time delivery rate, cost per order, and customer feedback. These metrics not only ensure performance assessment, analysis, and identification of bottlenecks, inefficiency, or waste, but also enable cost monitoring.
The benefits of using a WMS system for this purpose include:
Reduction of operating expenses.
Optimization in the use of resources.
Minimizing errors.
Improved customer satisfaction.
WMS: the key to accurate and efficient shipping
By now, you may have noticed how much of a competitive advantage the WMS system provides when it comes to shipping. It’s not just about ensuring accuracy and agility in the process, but also about ensuring compliance with standards and achieving various savings.
This is why experts are categorical in stating that companies that want to gain notoriety and conquer a larger space in the market cannot underestimate the power of WMS to optimize their logistics operations.
If you are interested in improving your warehouse’s shipping performance with a customized WMS system, our dedicated team is on hand to provide guidance and solutions tailored to your specific needs.
Contact us today to learn more about how to increase the efficiency and accuracy of your shipping and thus achieve even greater prominence in the market. Together, let's transform your logistics operation into a strategic asset for the success of your business!
Kommentarer